China Injection Molding for Beginners
Wiki Article
The Ultimate Guide To China Injection Molding
Table of ContentsSome Known Facts About China Injection Molding.The 8-Minute Rule for China Injection MoldingOur China Injection Molding IdeasChina Injection Molding Fundamentals Explained
Injection molding is a complex production process. Using a specialized hydraulic or electric equipment, the procedure thaws, infuses and establishes plastic into the form of a steel mold and mildew that's fitted into the equipment.: once the process has been established and also examined, shot molding equipments can produce thousands of things per hour. Making use of electrical injection molding devices also makes the procedure relatively energy efficient.: if the process parameters are tightly regulated, the shot molding process can create thousands of elements promptly at a constant top quality.
: whether makers are looking for solid, tensile or extremely thorough components, the injection molding procedure has the ability to create them at an excellent quality continuously. This cost-effectiveness, performance as well as element high quality are just some of the reasons many sectors choose to make use of injection molded components for their products.
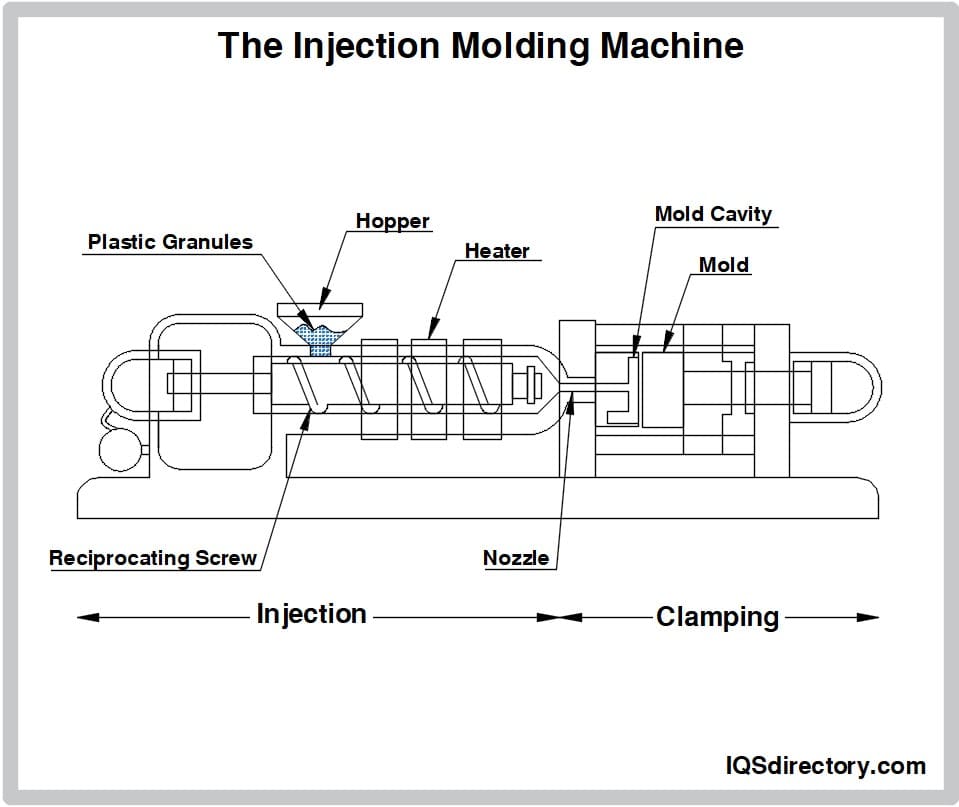
What Does China Injection Molding Do?
Each mold device is made up of two parts: the tooth cavity and the core. The dental caries is a set part that the plastic is infused into, as well as the core is a relocating part that suits the dental caries to aid create the element's last shape. Depending on needs, mold and mildew tools can be created to generate numerous or complex parts.Due to the high level of layout and quality of materials involved, creating mold and mildew tools is a lengthy and expensive process. These devices can be made use of to digitally create or create a prototype mold that can after that be tested in the maker with the chosen polycarbonate.
As soon as the ideal thermoplastic as well as mold and mildew have actually been checked and also selected, the injection molding procedure can begin. At their the majority of fundamental degree, these machines consist of a feeder or 'receptacle' at the top of the machine; a long, round heated barrel, which a large shot screw sits in; an entrance, which sits at the end of the barrel; and the selected mold tool, which the gateway is attached to.
As the screw turns, these pellets are fed progressively into the barrel of the equipment. The switching of the screw and the heat from the barrel progressively warm and also melt the polycarbonate up until it is thawed. Keeping the right temperature levels within this component of the procedure is crucial to making certain the plastic can be injected effectively and also the last part created properly.
Fascination About China Injection Molding
This draws through a collection quantity of plastic and also builds up the pressure in the screw prepared for injection. At the same time, both parts of the mold and mildew tool close with each other and also are held under high stress, called clamp pressure. Injection stress and clamp pressure must be stabilized to ensure the part creates appropriately which i loved this no plastic gets away the tool during injection.
This is referred to as 'cooling time', it can additionally range from a few secs to some mins and also makes sure that the part establishes properly prior to being ejected and also completed on the assembly line. After the holding and cooling times have actually passed and also the component is mainly developed, pins or plates expel the parts from the device.
In some situations, ending up procedures such as sprucing up, passing away or eliminating excess plastic (recognized as stimulates) might be called for, which can be finished by other machinery or drivers. As soon as these procedures are complete, the parts will be ready to be evacuated and dispersed to suppliers. Exactly how Essentra Components makes use of injection molding At Essentra Parts, injection molding is a key manufacturing process.
Some Known Incorrect Statements About China Injection Molding

What is Shot Molding? Shot Molding is a manufacturing process for creating parts in huge quantity. It is most usually made use of in mass-production procedures where the very same component is being produced thousands or perhaps numerous times in succession. Why You Might Wish To Utilize Shot Molding The major benefit of shot molding is the ability to range production en masse.
The price also tends to visit this site drop considerably as more parts are produced. Various other advantages include the following: Low Scrap Rates with Injection Molding Shot molding produces low scrap rates family member to standard manufacturing processes like CNC machining go to website which cut away significant portions of an original plastic block or sheet. This nonetheless can be an unfavorable about additive production procedures like 3D printing that have also reduced scrap rates.
Report this wiki page